Molded foam has applications in a wide range of industries, including: sports and recreation, lawn and garden, automotive fabricating, footwear and comfort, food processing, construction office, outdoors, mining and bath. Read More…
The applications for foam fabricating are only limited by one’s imagination; that is our slogan at American Excelsior. We are a foam supplier who offers many different foam cushions & foam padding for over a dozen industries.
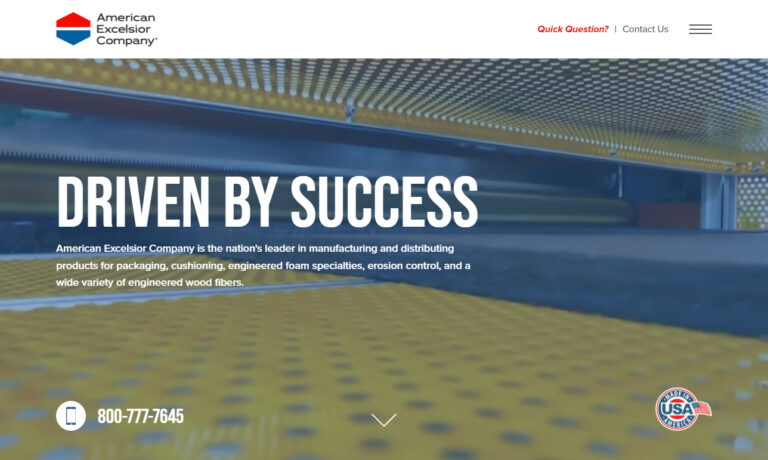
Since 1992, Flextech has delivered innovative, custom engineered foam solutions. We combine our engineering and design services with our unique foam lamination, fabrication, and thermoforming capabilities, to provide quality foam components to a diverse customer base. Our customers include OEM’s in the medical, industrial, military, aerospace and consumer products markets. We invite you to...
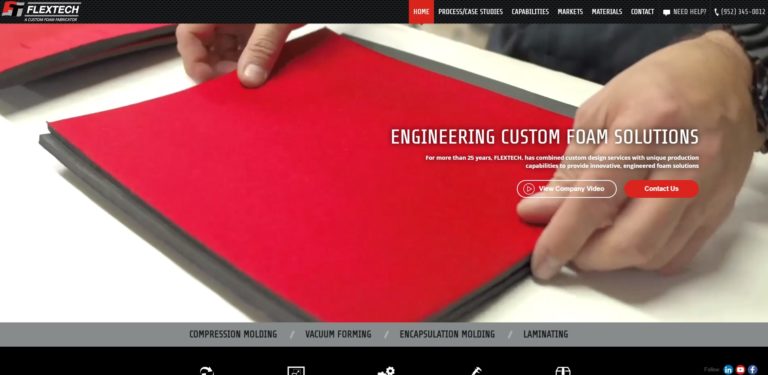
Deluxe Packaging works hard to always create cost-effective solutions and services for our clients better than anyone else. We offer a full array of high quality products, including polyurethane foam, polystyrene foam, and polyethylene foam. Our products are customizable to match a product’s fragility and size. Deluxe Packaging is your complete packaging solution provider for all of your...
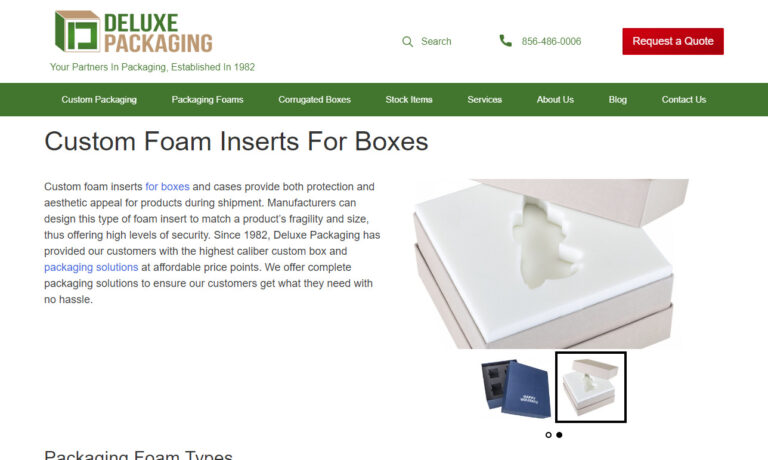
Here at Thrust Industries we provide die cut foam that comes in a variety of shapes and configurations. We die cut foam from a number of materials including: urethane, PVC, polyester, neoprene, ether, cellular, volara, and much more.
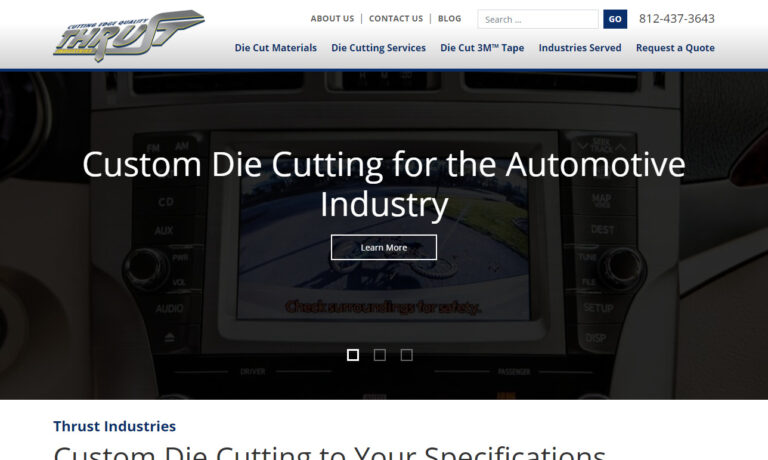
More Molded Foam Companies
Fabricators can mold polymer foam, such as urethane foam or polyethylene foam, into a wide variety of products, such as: molded foam sheets, bumpers, conveyor bushings, conveyor wheels, pneumatic seals, knee pads, helmet lining, mats and countless other products.
When designing your product, fabricators consider factors like: application environment, required impact resistance, required chemical resistance, required impermeability and more. Based on your application specifications, they can pick a material and a molding method. Each molding method has something a little different to offer.
Injection molding, for example, is inexpensive and capable of producing high volumes of high tolerance, complex parts. Unfortunately, though, the cost of cooling injection dies is quite high in comparison with the rest of the process. Also, the parts often require secondary processing after molding.
Reaction injection molding is unique in that it completes curing while the foam is still inside the mold. The foam, which is first mixed with additives (catalysts, polyols, surfacents, blowing agents, etc.) reaches the mold after fabricators inject it as a liquid. Once the liquid polymer is inside the mold, fabricators use an impinging mixer to pressurize it and give it its final shape. This type of foam molding creates lightweight and strong products, has low tooling costs and requires less clamping force than other molding processes. Its only real drawback is the fact that it has higher than normal raw material costs and high cycle times.
Centrifugal molding involves rotating the polymer material on an axis, where it’s exposed to centrifugal forces that help shape it. Fabricators use centrifugal molding to create products with large cross sections. It, however, is more time consuming than the other foam molding methods.
Whatever method your fabricators choose to make it, molded foam is an excellent investment for many customers. To find out if molded foam is right for you, consult with one or more of the many molded foam fabricators listed on this page.